Premium Screen Printing Kit for Business Startups
Premium Screen Printing Kit for Business Startups
Blog Article
Display Printing Uncovered: Everything You Need to Find Out About Tee and Garment Printing Methods
Display printing is an interesting technique that combines art with method, using countless opportunities for imagination. Ready to explore the essential components that make screen printing an art type?
The Basics of Display Printing: Exactly How It Functions
When you dive into screen printing, you'll uncover it's both an art and a scientific research. At its core, display printing includes developing a stencil, or screen, that allows ink to pass with just in certain locations.
Following, you'll blend your inks and prepare your printing surface. Position the display over the fabric, then utilize a squeegee to press ink with the screen onto the garment. This process calls for accuracy, as you desire clear, vibrant prints. After printing, you'll heal the ink with warmth, guaranteeing it follows the textile and lasts through cleans. Each step is vital, and mastering them will certainly boost your display printing skills, changing simple garments into distinct, meaningful pieces.
Kinds of Display Printing Techniques
Once you grasp the essentials of screen printing, it's time to discover the various methods that can elevate your designs. One preferred approach is traditional screen printing, where ink is pushed with a stenciled screen.
Another option is plastisol printing, understood for its durability and dazzling colors, making it a favorite for several brands. Experiment with halftone printing to develop gradient impacts and detailed styles.
Vital Equipment for Display Printing
To achieve magnificent results in display printing, having the appropriate tools is basic. You'll require a durable display printing frame, which holds the mesh that moves your layout onto the garment. Next off, spend in premium mops; these are necessary for using ink equally across the screen.
Selecting the Right Inks and Materials
When picking inks and materials for screen printing, you need to take into consideration the sort of ink that works best for your job. Think of textile compatibility to ensure your designs look terrific and last long. Explore green ink options to make your printing procedure more sustainable.
Types of Screen Inks
Selecting the right display ink is important for achieving vibrant, long lasting prints that meet your job's demands. There are several kinds of display inks to analyze. Plastisol ink is prominent for its convenience and convenience of usage, giving excellent shade opacity on dark textiles. Water-based ink, on the other hand, uses a softer feel and is green, making it perfect for those aiming to lessen their environmental impact. Release inks get rid of dye from the textile, causing a soft, classic look but require certain handling. Specialized inks, such as metallic or glow-in-the-dark, can add one-of-a-kind impacts to your designs. Review your job demands and select the ink that aligns ideal with your desired end result.
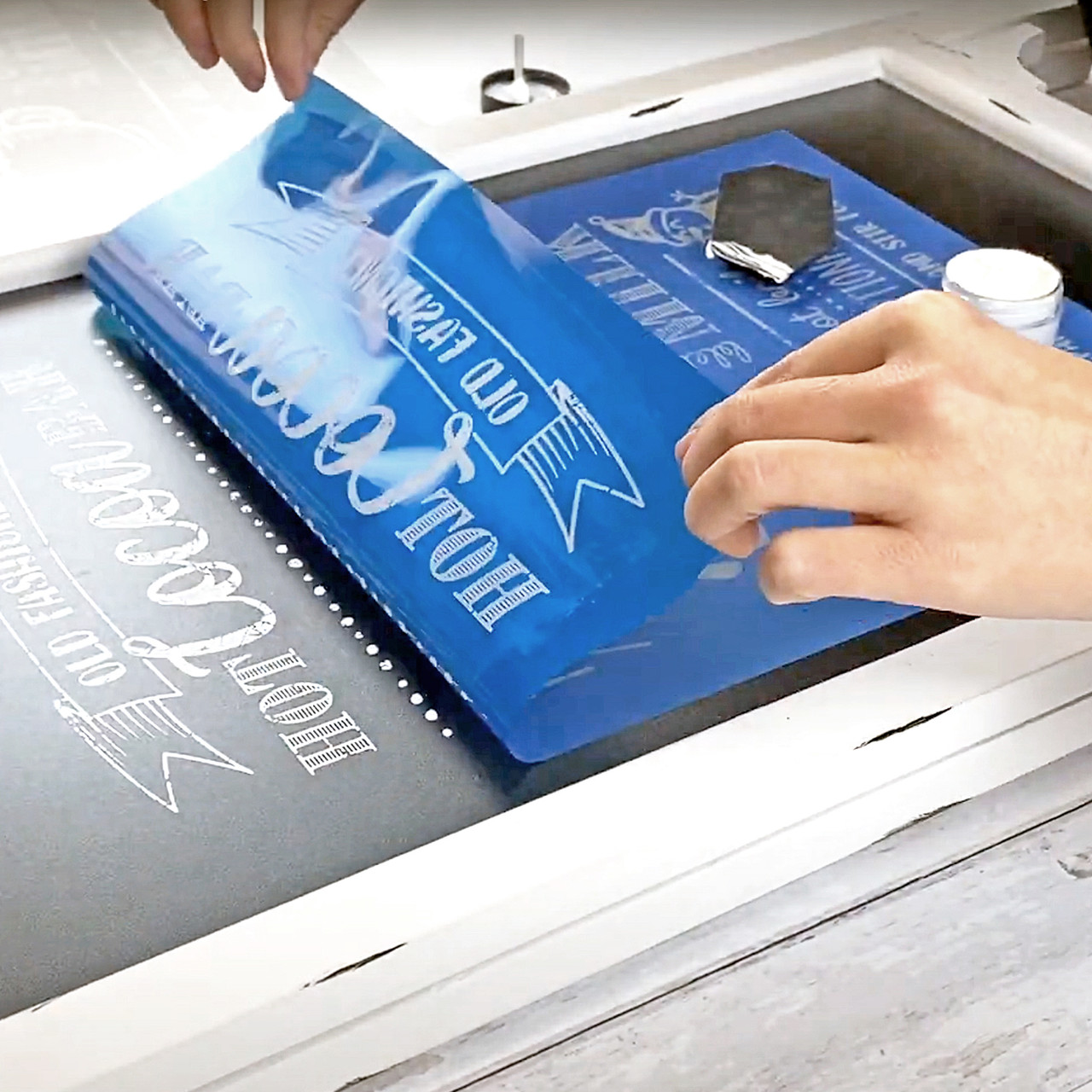
Material Compatibility Factors To Consider
Recognizing textile compatibility is important for achieving top notch display prints, specifically since various materials react uniquely to numerous inks. When choosing inks, consider the material type-- cotton, polyester, or blends. For cotton, water-based inks function well, using gentleness and breathability. Polyester, on the other hand, often calls for plastisol inks for much better attachment and vivid shades. You could need to utilize a combination of both kinds if you're publishing on blends. Constantly test your inks on sample material to assure they adhere correctly and keep shade integrity. In addition, bear in mind that material weight and texture can influence the final result, so picking the ideal ink and product combination is crucial for your task's success.
Eco-Friendly Ink Options
Environment-friendly inks are becoming a popular option for display printers that want to decrease their environmental impact while preserving high quality. When choosing inks, take into consideration water-based inks, which are less harmful and much easier to cleanse up contrasted to standard solvents.
Furthermore, try to find inks made from eco-friendly sources, such as soy or vegetable-based choices. By picking the right inks and materials, you'll not only create sensational layouts however also add to a much more sustainable printing process. Make the switch, and your prints will certainly reflect your commitment to the environment!
Preparing Your Layout for Display Printing
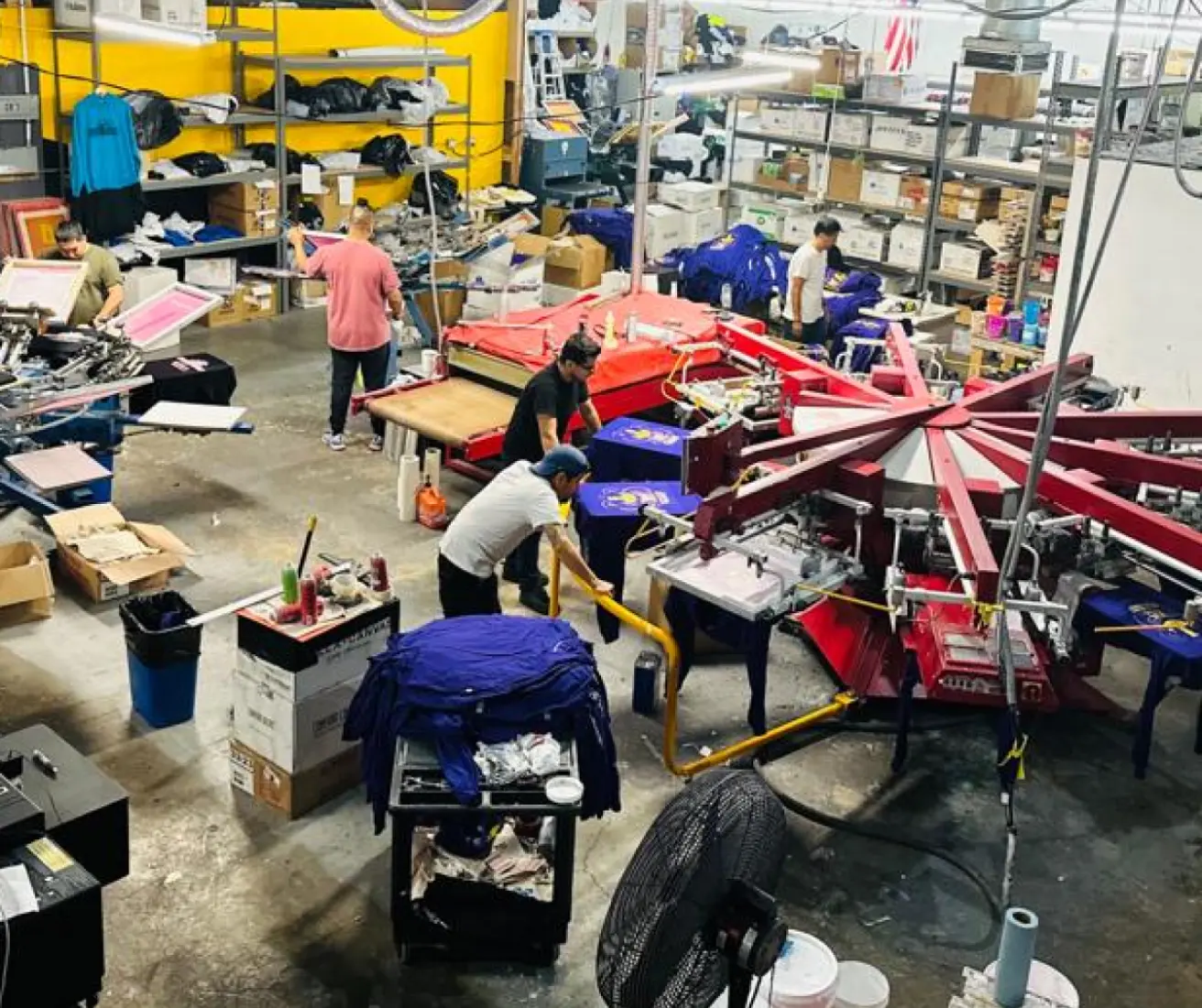
File Layout Demands
To link assure your design looks sharp and vibrant on fabric, you'll require to pay attention to file format needs for display printing. Beginning with vector documents like AI or EPS, as they can be scaled without losing quality. If you make use of raster images, choose high-resolution documents, such as TIFF or PNG, preferably at 300 DPI. Prevent utilizing JPEGs, as they can shed quality when resized. Likewise, make certain your style has a transparent background to stop unwanted white edges on your prints. Finally, maintain color settings in mind; CMYK is conventional for screen printing, so transform your RGB designs accordingly. By complying with these guidelines, you'll establish your artwork up for an effective print.
Shade Splitting Up Techniques
Shade separation is a vital step in preparing your design for screen printing, and grasping it can substantially enhance your print high quality. You'll need to break your design into specific colors, as each color requires a different screen during printing. This precision not just guarantees accurate color representation yet likewise simplifies the printing process.
Resolution and Dimension
Accomplishing the very best outcomes in display printing starts with ensuring your design has the right resolution and size. Preferably, your artwork needs to be at least 300 DPI (dots per inch) for sharp, clear prints. Your final item may look amateur and pixelated. if you make use of lower resolution.
When it pertains to size, take into consideration the measurements of your print area. Design your artwork to match the last print size, ideally developing it in the real dimensions you'll be printing. In this manner, you'll stay clear of any type of unexpected scaling problems.
Constantly check your design in both vector and raster styles. Vector graphics can be scaled without shedding top quality, making them perfect for display printing. Preparing correctly will assure your layout looks impressive on every garment!
Step-by-Step Display Printing Process
Screen printing is a dynamic procedure that enables you to produce dynamic designs on various surface areas. To obtain begun, you'll need a screen, emulsion, and your chosen ink.
After rinsing the unexposed solution, your screen is ready. Set it up on your printing surface area and straighten your garment underneath it. Pour ink onto the display and utilize a squeegee to press the ink with the stencil onto the textile. Lift the display carefully and let the print completely dry. Ultimately, treat the ink utilizing warm to ensure longevity. That's it! You have actually successfully screen published your design.
Tips for Successful Display Printing Projects
While you're diving into your screen printing jobs, keep in mind that prep work is key to success. Beginning by collecting all your click to investigate materials-- inks, screens, squeegees, and garments. A clean work area assists stop unwanted errors, so clean prior to you start.
Following, validate your artwork is high-resolution and properly sized for your garment. Check your screen for proper direct exposure and tidy it completely to prevent smudges. When mixing your inks, follow the producer's guidelines to attain the appropriate consistency.
During printing, apply even pressure with your squeegee for constant results. Don't hurry; take your time to confirm each print fulfills your requirements. After printing, let your garments dry entirely before managing or packaging them.
Lastly, constantly keep a sample of your job for future recommendation. By doing this, you can assess your development and boost your techniques over time. Happy printing!

Regularly Asked Concerns
Just how Lengthy Does It Require To Establish a Display Printing Job?
Establishing up a screen printing job generally takes about half an hour to an hour. You'll prepare the screens, mix inks, and change journalism. The moment differs based upon intricacy and experience, so stay arranged!
Can I Publish on Various Fabric Keys In Making Use Of the Exact Same Technique?
Yes, you can publish on various textile types utilizing the exact same strategy, yet you'll need to change your setups and inks. Some materials soak up ink in different ways, so experimenting guarantees the most effective results for each product.
What Are Usual Mistakes to Prevent in Display Printing?
When screen printing, stay clear of typical mistakes like using the incorrect ink, ignoring correct direct exposure times, or missing pre-press checks. Always evaluate your arrangement and keep tidy screens to ensure high quality results each time.
Just How Can I Properly Tidy and Preserve My Screen Printing Devices?
To properly clean and preserve your display printing equipment, you should frequently wash screens with ideal solvents, inspect squeegees for wear, and assure all tools are kept dust-free and completely dry. Uniformity stops pricey repair work and improves efficiency.
Is Display Printing Eco Friendly Compared to Other Techniques?
Display printing can be extra ecologically pleasant than other methods, particularly if you make use of eco-conscious materials and water-based inks. By picking lasting products and practices, you lower waste and decrease your effect on the browse around these guys earth.
Screen Printing Uncovered: Everything You Required to Know About Tee and Garment Printing Strategies
At its core, screen printing involves producing a stencil, or screen, that enables ink to pass via just in certain areas. Setting the display over the fabric, after that use a squeegee to press ink via the display onto the garment. One popular approach is traditional screen printing, where ink is pressed through a stenciled display.When selecting inks and materials for screen printing, you need to take right into account the kind of ink that works finest for your task.
Report this page